Adapter les machines tournantes
pour répondre aux défis opérationnels d’aujourd’hui
Le contexte économique actuel exige que les équipements de production soient plus flexibles que jamais.
Les pompes, les compresseurs et les turbines à vapeur jouent un rôle clé.
Les machines tournantes peuvent être optimisées pour répondre aux défis industriels actuels tels que la réduction des coûts d’exploitation, la flexibilité opérationnelle, l’augmentation de l’efficacité et de la fiabilité. Voici comment :
Pompes
Certains ajustements techniques sont nécessaires lorsque l’on modifie les conditions d’exploitation, comme l’augmentation ou la réduction de la capacité et/ou le changement de la densité du produit. En fonction de la technologie de la pompe et des nouveaux objectifs de performance, plusieurs options peuvent être envisagées.
De nouveaux objectifs tels que la hauteur de refoulement, le débit ou de nouvelles conditions de fonctionnement du procédé peuvent être atteints en modifiant les composants internes, par exemple en redimensionnant la roue pour maintenir le nouveau point de fonctionnement au meilleur point d’efficacité tout en réduisant de manière significative la consommation d’énergie électrique.
Pour les pompes multi-étages fonctionnant à grande vitesse et entraînées par un moteur à vitesse fixe, le changement de rapport d’engrenage peut être un moyen alternatif d’atteindre le nouveau débit requis par le procédé sans modifications majeures de la pompe.
En outre, le remplacement d’un moteur électrique existant peut être envisagé dans les cas suivants :
- Le moteur devient surdimensionné en raison d’un fonctionnement durable à faible débit (efficacité énergétique dégradée).
- La différence entre la puissance nominale et la nouvelle puissance demandée, ainsi que la marge d’échauffement des enroulements, devient trop étroite (fonctionnement en surcharge).
D’une manière générale, chaque fois qu’il y a un changement dans les paramètres du procédé, une analyse doit être effectuée pour évaluer les aspects hydrauliques (limites de NPSH et de débit minimal pour le fonctionnement, dimensionnement minimal de la vanne), électriques (classe d’échauffement (pour les enroulements) et mécaniques (limites de vibration à faible débit et à grande vitesse).
Compresseur centrifuge
Les compresseurs centrifuges sont conçus pour des paramètres de procédé donnés (pression, température, poids moléculaire, débit massique) à une vitesse nominale avec une conception spécifique de la roue et des internes.
Ici aussi, en cas de modification importante des paramètres du procédé, une revue de la conception doit être effectuée afin d’éviter des dommages importants au compresseur ou à la machine d’entrainement, lorsqu’ils fonctionnent en dehors de leur fenêtre de fonctionnement. Cela peut typiquement se produire lors d’un fonctionnement à faible débit (pompage) ou à débit élevé (surcharge).
Cet examen de la conception peut être effectué par une tierce partie autre que le fabricant de l’équipement d’origine.
Si les nouvelles conditions du procédé font sortir la machine de sa fenêtre de fonctionnement, une mise à niveau majeure peut être envisagée, mais dans de nombreux cas, aucune modification du corps n’est nécessaire.
L’installation d’une nouvelle cartouche (roues et internes dotées d’une nouvelle technologie de conception) permet d’obtenir une marge d’efficacité significative. Par exemple, une augmentation de 15 % du débit massique sans impact sur la consommation d’énergie électrique a été obtenue sur un compresseur de gaz humide d’une unité de craquage catalytique (voir photos 1 et 2).
Une autre option est l’examen des auxiliaires pour une mise à niveau complète en termes d’étanchéité (montage de nouvelles garnitures sèches) ou de protection contre le pompage (sélection d’une nouvelle soupape anti-pompage).
Dans tous les cas, le pré-assemblage en atelier est fortement recommandé pour minimiser la durée de l’intervention sur site pendant le délai d’exécution.
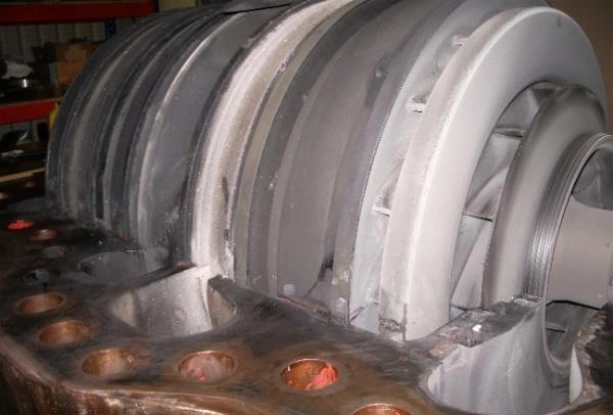
Photo 1 – Corps de machine avant modifications
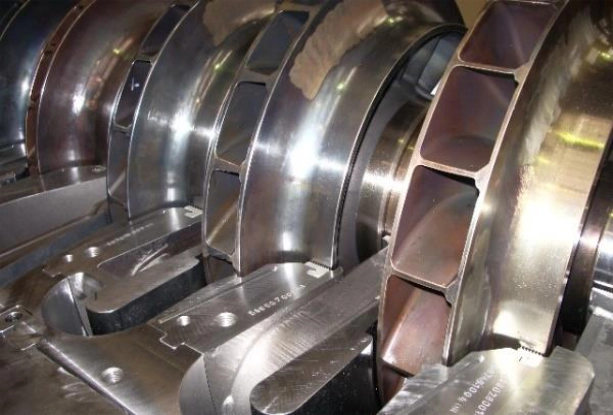
Photo 2 - Même corps de machine après modifications, avec de nouveaux internes et un nouveau rotor
Compresseur à piston
L’adaptation à de nouvelles conditions de procédé est plus facile à mettre en œuvre et moins coûteuse pour un compresseur à piston, car il est possible d’ajuster soit la course, soit le diamètre du piston, soit la vitesse de rotation.
Voici quelques exemples de la manière d’obtenir un débit plus faible ou plus élevé :
suit :
- Dans la plupart des cas où le bâti du compresseur est surdimensionné, il est possible de modifier le débit en ajustant la vitesse de rotation sans apporter de modifications majeures au compresseur.
- Un nouveau rapport d’engrenage peut suffire à répondre aux nouvelles exigences de performance pour les compresseurs entrainés au travers d’un réducteur équipés d’un moteur ayant une marge de puissance suffisante.
- Pour les compresseurs à entraînement direct, l’utilisation d’un nouveau moteur électrique avec un nombre différent de pôles permettra d’atteindre la nouvelle vitesse et la nouvelle puissance requises.
- Une autre façon d’augmenter ou de réduire le débit consiste à remplacer soit le piston et la chemise (nouveau diamètre), soit le vilebrequin (nouvelle course).
Dans tous les cas, il convient d’accorder une attention particulière aux bouteilles et aux membranes de protection contre les pulsations, et le système doit donc être soigneusement vérifié.
Si le compresseur est équipé d’anciens dispositifs de contrôle du débit pas à pas, la nouvelle technologie des dispositifs de contrôle du débit électro-hydraulique sera installée afin de réduire la consommation d’énergie électrique. (Photo 3).
Turbine à vapeur
Une revue de la conception des éléments internes (aubes et diaphragmes) doit être effectuée si la puissance de sortie est modifiée ou si les conditions de vapeur diffèrent de la conception initiale (pression, température, contre-pression ou vide) ou encore si le fonctionnement de la fenêtre de vitesse diffère de celui d’origine.
This review is mandatory if speed window operation differs from the original one. This will prevent blades failure (overloading) or rotor damages (overspeed).
La conception de nouvelles vannes d’admission ou la modification de la définition du trajet de la vapeur (aubes et diaphragmes) sont les meilleures options pour améliorer les performances et la fiabilité de la turbine.
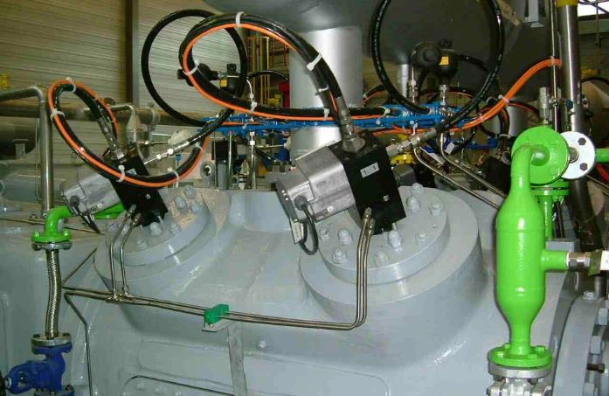
Photo 3 – Nouveau dispositif de contrôle du débit électro-hydraulique
Il est possible de réduire la puissance de sortie en diminuant la surface de la buse d’entrée de la vapeur.
Des méthodes de réparation spéciales doivent être appliquées si le rotor existant a été endommagé afin de restaurer toutes les performances de la turbine (réparation des disques, soudage pour la fixation de nouvelles pales).
Enfin, les pièces de rechange d’occasion (internes et rotor) constituent une option intéressante pour redémarrer les opérations en quelques semaines après un incident majeur.
Soufflante d’air
Les modifications de la soufflante d’air peuvent être effectuées par un tiers après évaluation des nouvelles performances. Il existe plusieurs options pour augmenter la capacité, soit en changeant la roue, soit en adaptant la vitesse du moteur.
Une étude détaillée doit être menée pour déterminer la meilleure stratégie. Parfois, un simple changement d’une ou plusieurs roues plus efficaces est possible, même sans changer le corps existant. Un contrôle spécial de la machine entrainante est nécessaire : Pour la turbine (puissance et couple maximaux), ou la capacité du moteur électrique.
Chaque cas doit être analysé à la lumière de la data sheet originale et des courbes de performances afin de déterminer s’il vaut la peine de modifier la soufflante ou la machine entrainante.